Let us look at a simple teaching example:
Dump Truck Accident Example
Ajax Construction Company was awarded a contract to build a condominium on a hill overlooking the city. Prior to initiation of the project, a comprehensive safety program was developed covering all aspects of the project. Construction activities began on Monday, October 4, 1978, and proceeded without incident through Friday, October 8, 1978, at which time the project was shut down for the weekend. At that time, several company vehicles, including a 2 1/2 ton dump truck, were parked at the construction site. On Saturday, October 9, 1978, a nine-year-old boy, who lives four blocks from the construction site, climbed the hill and began exploring the project site.
Upon finding the large dump truck unlocked, he climbed into the cab and began playing with the vehicle controls. He apparently released the emergency brake, and the truck began to roll down the hill. The truck rapidly picked up speed. The boy was afraid to jump out and did not know how to apply the brakes. The truck crashed into a parked auto at the bottom of the hill. The truck remained upright, but the boy suffered serious cuts and a broken leg. The resultant investigation revealed that, although the safety program specified that unattended vehicles would be locked and the wheels chocked, there was no verification that these rules had been communicated to the drivers.[1] An inspection of the emergency brake mechanism revealed that it was worn and easily disengaged. It could be disengaged with only a slight bump. There had been no truck safety inspections or requests to adjust the emergency brake linkage.
Several observations can be made regarding this event. For example:
The truck driver did not chock the wheels of the truck
The emergency brake is worn and easily disengaged
Step 1
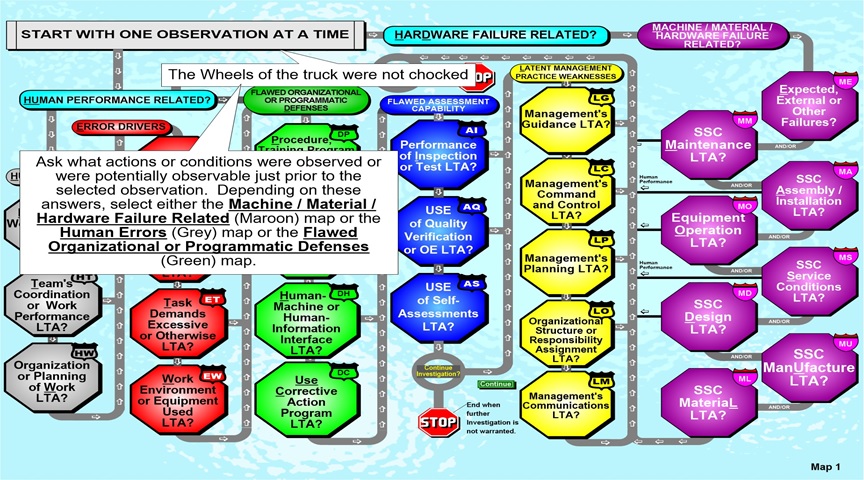
We will first evaluate the observation that “The driver did not chock the dump truck’s wheels” using the Cause Road Map.
Step 2 – Human Error
Answering the question “Was coordination or interaction with or between task performers of with supervision inappropriate or inadequate for the task?” from Cause Road Map 2 aided with details from the Coordination or Coaching (Code HTCC) entry in Table 3-1 results in the conclusion that “Neither the driver nor anyone else was tasked with locking and chocking vehicles.”
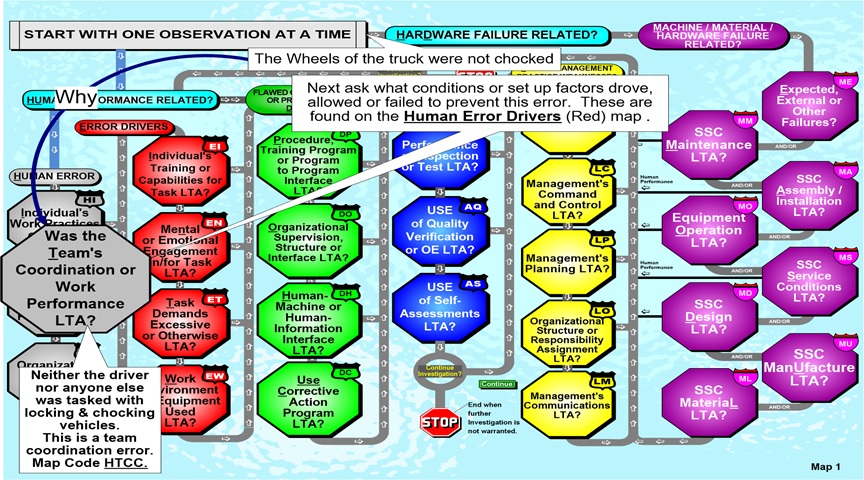
Step 3 – Error Drivers
Answering the question “Was the task performer’s knowledge or experience level inappropriate for the task?” from Cause Road Map 3 aided with details from the Lack of knowledge (inadequate training) (Code EITT) entry in Table 3-3 results in the conclusion that “The driver had not attended a Driver Safety Training course.”
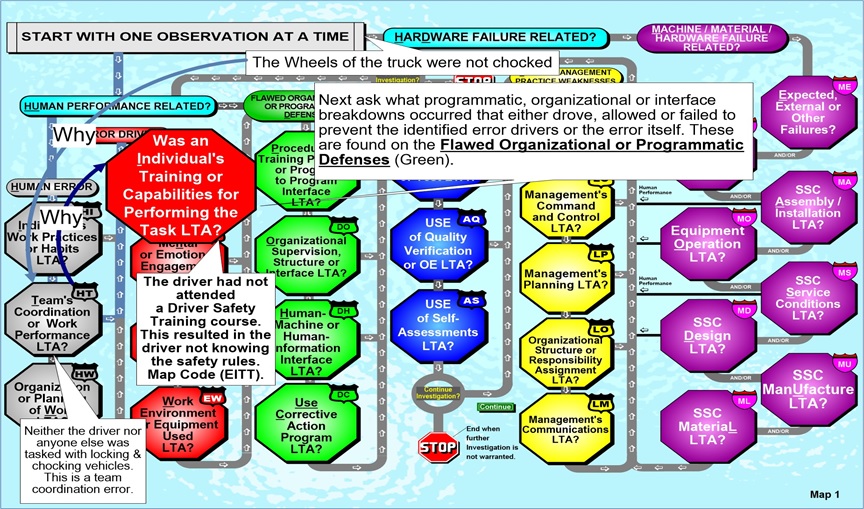
Step 4 – Flawed Organizational or Programmatic Defenses
Answering the question “Why was needed training not given?” from Cause Road Map 4 aided with details from the Training Breakdowns (Code DPTN) entry in Table 3-4 results in the conclusion that “No Driver Safety Training courses were scheduled or given.”
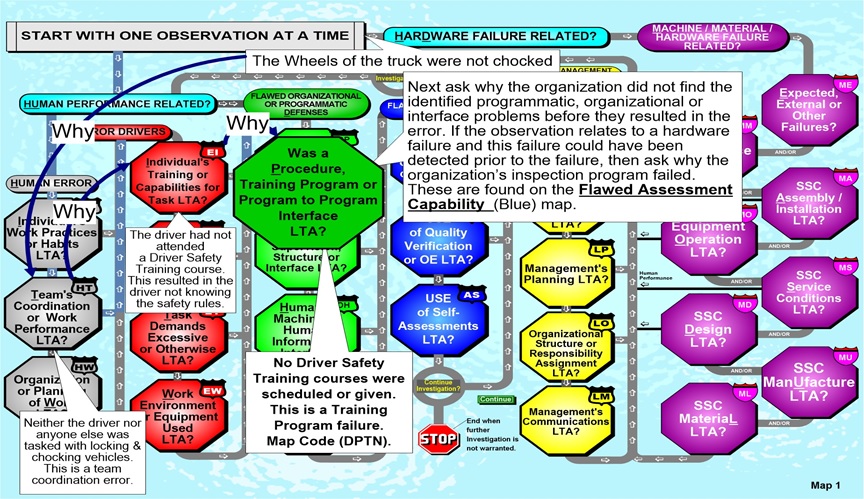
Step 5 – Flawed Assessment Capability
Answering the question “Was use of Self-Assessments to improve performance LTA?” from Cause Road Map 5 with details from the Self-Assessment planning, use and rigor (Code ASAS) entry from Table 3-5 results in the conclusion that “The company did not monitor safety program infractions or training attendance. This is a significant loss of performance monitoring capability.”
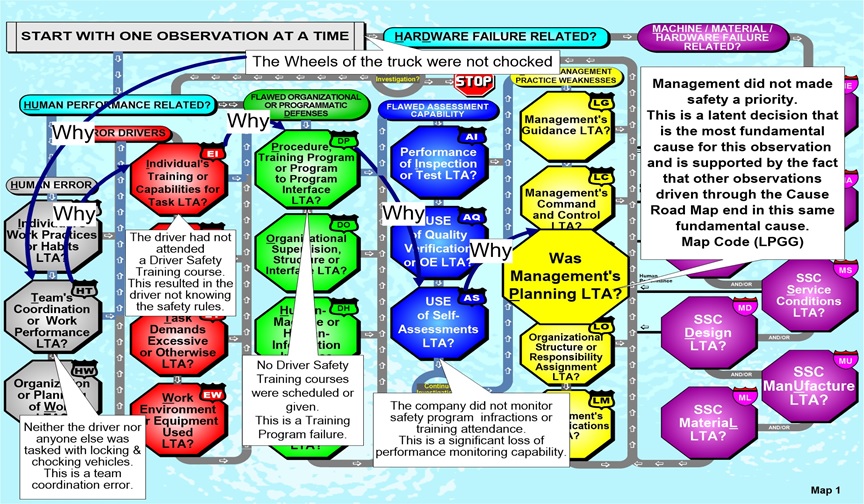
Step 6 – Latent Management Practice Weaknesses
Answering the question “Was Management’s Planning LTA? from Cause Road Map 6 with details from the Management Planning Decisions entry (Code LPGG) from Table 3-6 results in the conclusion that “Management did not made safety a priority.”
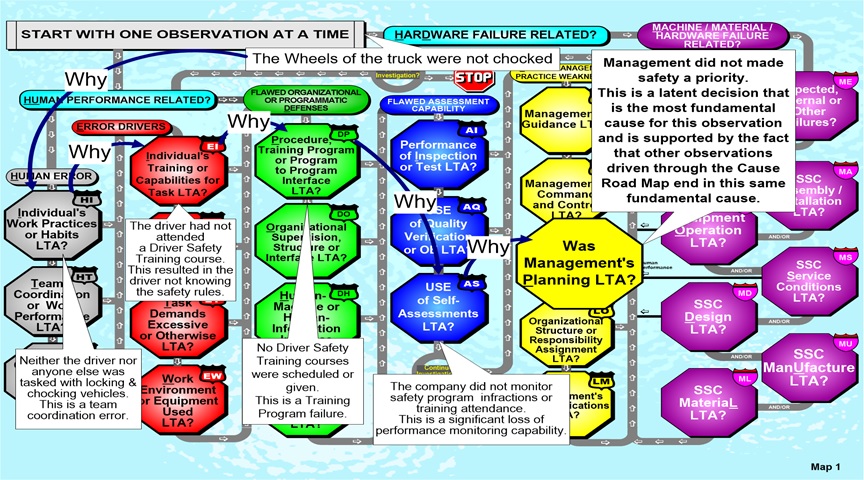
The conclusion that the company’s management team had not made safety a priority is supported by a documented trail of facts. By using a systematic approach to find the basic cause(s) for the event, appropriate actions can be taken to prevent a future similar event.
Step 7 – Safety Culture
The conclusion that “Management did not make safety a priority” is as far any other popular root cause methods will get you. If fact, because a member of the company’s management team is typically the sponsor for the cause investigation, asking this kind of question is often discouraged. The next figure uses the Cause Road Map to ask why the management team did not make safety a priority.
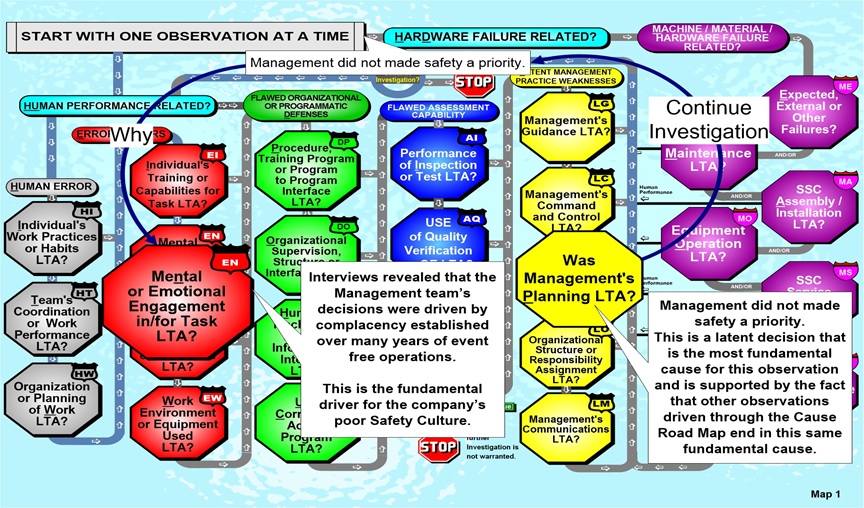